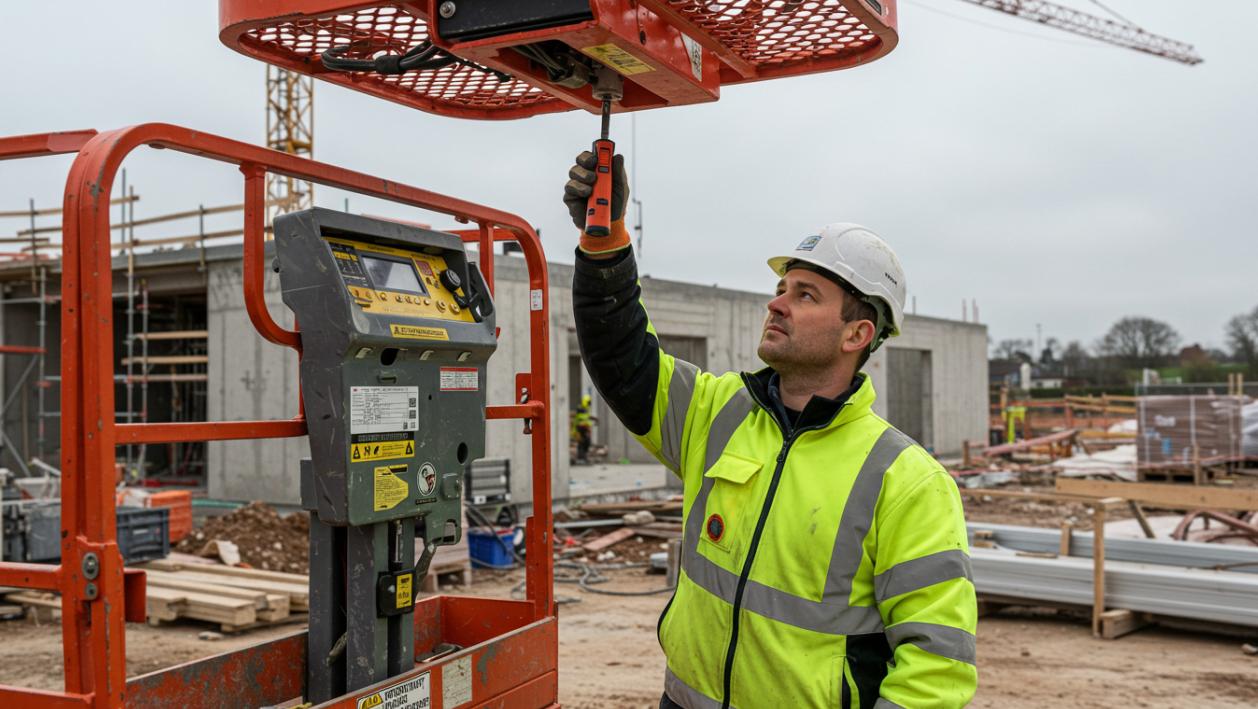
Ensuring the safety of lifting equipment is not just a regulatory requirement but a vital aspect of preventing serious injuries. LOLER regulations dictate comprehensive inspections and maintenance protocols that every employer must adhere to. With tens of thousands of accidents linked to faulty lifting equipment annually, knowing how to properly inspect and maintain these systems can make all the difference in protecting lives and ensuring operational efficiency.
Understanding safety standards
Safety standards for lifting equipment vary across regions and industries, but they all have one common goal: to protect personnel and property. Operators and stakeholders must familiarize themselves with the relevant laws and guidelines.
Legislative framework for lifting equipment
In many jurisdictions, regulations such as the Lifting Operations and Lifting Equipment Regulations (LOLER) provide guidelines for safe lifting. These regulations necessitate thorough inspections that aim to meet strict safety criteria. Understanding these frameworks aids organizations in safeguarding their workforce while reducing legal liabilities.
Importance of compliance
Compliance with safety standards is not merely a legal requirement but also a commitment to operational excellence. Organizations that uphold these standards foster a culture of safety that enhances employee morale and productivity. Equally, adhering to safety regulations can prevent costly accidents and damage to equipment.
Essential mandatory checks
Regular checks are critical in maintaining the integrity of elevating gear. These inspections prolong the lifespan of equipment, contributing to overall operational efficiency.
Types of inspections required
The essential inspections include:
- Pre-use inspections: simple checks that operators conduct before every use to identify visible wear and tear.
- Periodic inspections: these are scheduled checks that may occur weekly, monthly, or quarterly, depending on equipment usage.
- Thorough examinations: conducted by a competent individual, these are comprehensive assessments to identify safety-critical issues and are required at least annually.
A competent person is defined not by titles but by their knowledge, experience, and impartiality. This individual should be expertly qualified to identify possible defects, assess risks, and suggest appropriate measures for safe operation. Organizations often benefit from engaging external partners as a way to ensure independence and optimize the integrity of the inspection process.
Understanding thorough examinations
Thorough examinations serve as the backbone of safety compliance for lifting equipment. These checks are systematically performed by certified individuals for ensuring the safe operation of lifting equipment.
Scheduling thorough examinations
The frequency of these thorough examinations typically follows set intervals:
- Every 6 months: for equipment lifting individuals or associated accessories.
- Every 12 months: for other lifting equipment not associated with personnel.
Detailed evaluation criteria
The evaluation criteria during a thorough examination involve various safety checks, including:
- Visual inspections for any signs of damage or wear
- Functional checks to ensure all components operate correctly
- Measurements that assess the equipment’s integrity
In some cases, advanced Non-Destructive Testing (NDT) methods may also be employed for a more comprehensive assessment. Proper documentation of these examinations is vital, as records must be accurate, easily accessible, and protected from unauthorized alterations.
Record-keeping and reporting defects
Several essential obligations arise from conducting thorough examinations and inspections, particularly regarding documentation and understanding potential defects.
Maintaining records
Records of inspections and thorough examinations are crucial for compliance and safety management. This documentation must include:
- Dates of inspections
- Details of any defects found
- Recommendations for remedial actions
These records should be maintained securely and made available for inspection by relevant authorities when required.
Defect management
If defects are identified during inspections, immediate action must be taken to mitigate risks. The responsible personnel are required to notify relevant stakeholders and ensure that the equipment is taken out of service until rectifications are made. This proactive approach safeguards against potential accidents and protects the well-being of staff.
Lift inspection is vital for ongoing safety and following health rules. Regular checks by a skilled person are key to finding possible dangers and reducing risks when lifting things. By adopting robust safety practices, companies not only protect their workforce but also bolster efficiency and productivity.
Ensure the safety of your lifting operations. Contact a specialized company to carry out regular inspections of your elevator in compliance with current standards.
https://www.youtube.com/watch?v=WNfHVCtmDmQ